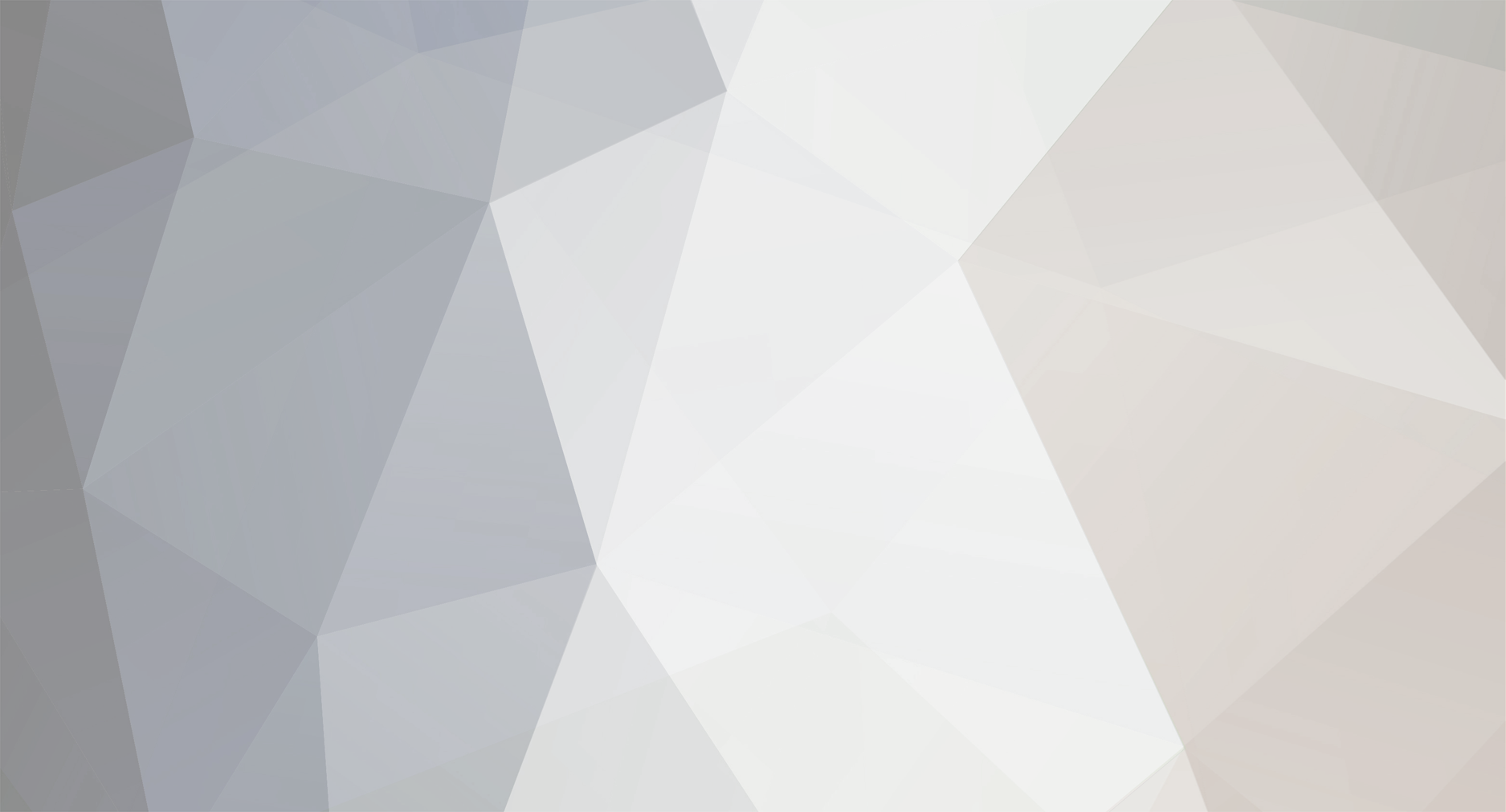
tugboat
Members-
Posts
27 -
Joined
-
Last visited
Content Type
Profiles
Forums
Events
Everything posted by tugboat
-
reader's digest version of all the spectra pull tests in one video....
-
http://www.youtube.com/watch?v=ODni9l8TLRw Old Spectra Web Find Baseline test Another baseline test....using a thinner shackle. 1st weathered test 2nd weather test 3rd weather test More to come/upload... including the "reaaders digest version of all the tests". lol.
-
Well Joseph...in my samples there has been no bending at all. The spectra just hung out in the weather for four years. And the new stuff from the same lot just sat on the spool for 7-8 years. Actually spectra's flex fatigue is pretty good from my studies. Kevlar, on the otherhand, being a fibourus aramid, has a significant flex fatigue problem compared to spectra. However,... i have found studies showing that nylon is superior to spectra in the flex fatigue department. In terms of Nylon having a longer more useable lifespan,.... i would think it all depends on the care taken with each product. Nylon has a tremendous shelflife as does Spectra. Nyoln has been shown to be able to absorb more punishment overtime due to its elasticity. But on the otherhand, if its not well cared for its no better than spectra or anything else for that matter....IMHO and tests. Indeed nylon does not endure the elements as well as spectra, but it does put up with flex better.
-
Ps....alll the webbing well kept webbing was off the spool and is about 7 or so years old.....from two differnet manufacturers/mills. Also note: that while i found a 33% drop in strength in the spectra blend slings.... i have found a greater decrease in nylon slings from weather exposure. Spectra, in my findings, does endure the elements better than nylon (as manufacturers quote and other lab test have shown.). But this only speaks to weather 'exposure' over a long period of time... nothing else. My test of pure spectra slings was to try and determine if the spectra was also being impacted upon by the elements,....or if the weak link in the spectra blend slings was just the nylon. So far, i have found that there is 'exposure' degeneration of spectra but not age degeneration. But i have found nylon weather exposure degeneration to be greater than spectra's. This is too only speak of spectra material compositions from eight years ago; not to make conclusions of newer formulations of spectra or dyneema. The spectra in my pure spectra slings was the same spectra being woven into specrta blend climbing slings of the time.
-
Ok. So i just finished 4 hours of pull testing my sewn up samples of weather exposed vs well stored spectra/nylon blend climbing webbing. I established a baseline strength of a well stored webbing sling,... and then busted about 8 weather exposed slings. THe exposed slings have never been used in climbing or loaded in any way...the material was just left outside for the last 4 years...year round. In general i found on average a 33% decrease in the weather exposed slings than the well stored, unused, sling material. Just for kicks, while i was at it, i broke some new Blackdiamond carabiners. And i broke some Kong carabiners. As well i did some more esoteric tests, like busting a single bartack, trying to bust knotted spectra blend climbing slings (two different mills webbings) and i busted some parachute buckles. I shot everything in high def 60fps. I just need to edity the footage and upload it to you tube for those of you interested. First though, i need some coffee and food....'cause that was alot of work! Should have it done in a couple hours.
-
Graham, you suggested that my tests of my pure spectra slings in no way resemble modern spectra blends. in terms of "modality", i may concende your point. However, the tests were only to look at and isolate spectra fiber aging by itself... not to replicate current climbing spectra blend slings. But in this manner i can't see any issues with my aged pure spectra destruction tests. Please point some out if you can see some. Now, today i found some of my old spectra/nlon blend climbing webbing that i got from the manufacturer, that had been left outside in the elements for the last 4 years. It is climbing webbing milled for a USA climbing gear manufacturer that the original mill allowed me to buy to test for my applications. For the gear companies privacy, i won't name them here. But suffice it to say, it is a,legitimate, mainstream climbing company. Now, i have the old weather exposed webbing, and i have this same original webbing lot, on the spool, at my shop. The spool was properly stored for the last 8 years, since i received it. So a sling destruction test of the exposed material and the original, well kept webbing material, should be a good age effect test, as regards the elements....no? On that note, im off to the shop now to tack up some slings for the test. Hopefully i can test them today too....if the darn rain doesn't start. I will post video of the pulls when i finish them. peace.
-
some accelerated aging tests by Dsm and Euro textiles dsm euro fiber and textiles
-
-
Hmmm.... Yes i remember reading the Tom Moyer article once before. However it doesn't study "exposure" variables. Apart from my semi-laymen testing, i have spoken with sailmakers of large racing sail making companies. They have atested to the excellent "exposure" properties that they have witnessed on ten year old sails. As well i have spoken directly to the manufacturers of both the spectra fibers i use and the material manufacturers that mill their product into the various forms i use... on the old spectra harness that i tested in the video... the results were much lower that i would have expected. The pic point i pulled had never been loaded before,...and normally i would not see the a straight out pull (90 degrees to the torso) break the attatchment point at under 6000lbs. In fact i would not see the standard Wichard shackle used for stunt work (of thinner diameter) cut thru ONE half of the the vectored spectra webbings until 5000 lbs. This would have been a "worst case scenario" usage of the pic point given that i was loading only one half of the pic vs all four webs of the attatchment points. In the video...one of the halves was sliced thru using a slighlty larger (than the typically used) wichard shackle at about 5000lbs. Assuming equal 4 way loading to all the strands, then the webbing was able to be cut the one half at 2500 lbs (a very low number that i have never witnessed before). Again that harness was one that had been left to the elements for about 4 years and was 8-9 years old since manufacturing. That old harness also did not have the tactile texture of the original materials. While it did not have the extreme "crunchy" feel of nylon after weathering....it did have the same suppleness of the original.
-
BY the way: Very nice Packs crackers:)
-
Crackers....not sure what your saying in your quote about sling "composition" ie nylon and poly, in regards to my posts?. Maybe you could expand on what you are trying to say there? The slings i busted were pure spectra as well as spectra/nylon blend (no poly), sourced directly from the manufacturers for rockclimmbing . You could be correct that there may be other "modalities" rather than exposure leading to the strength degradation... what do you suggest?... I just can't offer any other explanation since exposure and hand tied knots (not for climbing use) were all that the spectra was exposed to. I have more salvaged lengths of that weather exposed spectra webbing, so i will sew more of it up and test,...as you would be correct in saying that 1 or two slings don't make for a great sample pool. As well... the spectra/nylon 3/4 inch sling was milled for the climbing industry. Your points about DSM and Spectra are well understood. All my Spectra materials came straight from the manufacturers. (webbing, fabric and thread.... they are large, well know manufacturers from the USA (and one canadian broadcloth manufacturer) that supply both the climbing industry and military with spectra products.) Anyway, just wondering what other factor do you think could be contributing to the lower break number? I'm interested in your ideas as i did not expect the lower reading. .... Perhaps speed of pull generating heat? Or the slow speed of my pulls thus lending to creep or the theory of spectra's inital/first load exposure being lower than nylon? Anyway cracker's...my efforts here are to look at spectra itself,....not specific rock climbing products. Furthermore....all my research has led me to much "commercial" hype and statments of spectra's durability ....but very little long time, real world tests. That is what i am trying to provide with my testing. Do you have any mullen burst, or tougue tear etc type tests on new and aged spectra fabrics such as the cuban sailcloth (unwoven, fine strand spectra/mylar matrix)you use in some of your packs? Tests on old, well used samples, and new spectra? That would help us here. I have not found any lower strength numbers on aged, but well stored spectra,...just (to this moment, ostensibly) on the weather exposed spectra. Peace...
-
Well....time to eat some crow. While in the past i have found well used and exposed spectra to maintain significant strength (up to 90% in specific cases....not climbing); todays tests show definite loss of strength when exposed to severe, year round conditions (snow,rain,sun). I tracked down some 3-5 year exposed pure spectra and tacked some slings for testing and compared to new spectra. I only did a couple of tests. But i found that in general that the highly weather exposed spectra was 65-70 percent the strength of the new spectra sling. I also recordered the knot slipping potential of a hand tied spectra sling for anyone interested. Furthermore, what is interesting as regards spectra shelf life, is what i found looking back at the brand new spectra breaking strength as compared to today's "new" spectra sling comparison sample. The "new" spectra sling material from today was taken of the roll from a batch that i stored in good condions from eight years ago. Looking back at test samples from that eight years, i found there was no change in sling strength (at least when pulled over an 8mm pins (UiAA calls for 10mm) at all. In 2003 i measured samples breaking at 5450 pounds, and today at 5500lbs over the same shackles. here's links to the videos: [video:youtube] [video:youtube]
-
For those interested, i have started a Blog on Stunt harness manufacturing (as this is my area of expertise). Since i came from a climbing background and then transitioned into film work.... the Blog will have applicable material to climbing sewing theory and practice. The Blog is just in its infancy. But i will try to work and ad to it everyday for this interested in following. This blog is presented as educational/information source, rather than a promotion of my company. http://stuntharness.blogspot.com/
-
jfs1978, no problem...its academic and practical for me too. Since i need to know the academics to get my product and knowledge correct for the customer. I guess the main reason i piped up on the spectra life issue is that the question has been popping up in my industry. I now have product returning to me that is 8-10 years old. It's entirely made of spectra fibers, and people are replacing them with new harnesses. IN exchange i get to bust the old ones. I've been finding full to over 90% strength much of the time (not all the time) But ten years ago i built things way overkill (read; liability). As the years have past and advanced materials and engineering have progressed.....manufacturers have found that they can pass "standards" using less and less material. THis, while still strong, leads to "life" or "durability" issue. In a way that's how i see the thin "ultra tape" (nylon/spectra) blend sewn slings climber's are using: you can decrese the size and weight of the product and meet specs.....but at what longterm cost? Rock and Ice did an interesting arcticle that might apply here: http://rockandice.com/articles/how-to-climb/article/494-busted Also the reason i mentioned "before and after" tests....is that i have found, on occasion, that some slings, and several harnesses, dont meet there rated UIAA specs when bought brand new.... this can be for several reasons....that i wont go into here (it doesnt mean they are unsafe). So if you don't have a real world average before the test, the "after" number is based on someone elses #'s. its all academic at this point. The stuff is so over kill... In all my testing, climbing and building the number one thing i have learned is inspect your equipment regularly and leave at least 3-4 inch tails extruding from any "joint" eg tighed water knot, double passed buckle etc.... without this tail your putting yourself in danger. F
-
Remember "bartacking" is quite particular to the climbing industry.....originating from modified blue jean bartackers. There are pros and cons to bartacking. Too big a topic to get into here. But the majority of the safety sewn goods industry do not bartack (for good reasons)...They use safety stitches developed over years of proven technique in industries such as Parachuting, sailing, Rescue Harnesses, Rigging and so on. Bartacking has its place, but it can be used incorrectly esecially when strength sewing webbing to fabric. Box X and multi point "W" stitching can be superior depending on the circumstances... You don't need a bartacker to strength stitch in general. Another good book is the "Parachute Manual"
-
pfaff 138 is a newer model of the above mentioned pfaff...find them for between 500 and 1000$. They will run nylon or spectra 92 thread. They wont run 138.
-
some of my cherished machines....the pfaff is the best "all around".
-
A good industrial starting machine for you might be a pfaff 138 zig zag. Because its a two step zig zag, it will straighten out nice when you want to straight stitch. And this can be done on the fly,...zig zag to straight. It has a nice wide (6mm) zig zag, and is very well made, being originally from western germany. It was (and still often is) the machine of choice for parachute repairs, boat canvas work, and general tailoring. The machine has such cult following that they can be hard to track down. But once you own one you'll never go back. You may add machines, but you won't sell your 138. Expecxt to pay 1000$ for a mint newer one (cream color), and 500 for an older (black) TLC one. If your not seasoned at sewing and using your right hand as a brake....then you can swap out the clutch motor for a servo motor that has rpm control. Don't mess with swapping to pulley reduction unless your looking to maintain heavy punching power. The pfaff 138 is dogfeed vs walkingfoot/needlefeed. This has its pros and cons....but should be fine for your use. The above members' comments are all valid. you get what you pay for, and machines on the industrial level are built to do their one specific task (exculding pfaff 138). If your looking for a mechanical bartacker, really do your research here. You can spend good money on what you thought was a "deal" and end up with a machine that can't get the job done. For climbing sewing, you need to generally run size 138 nylon thread. Since older mechanical tackers were built for the blue jean industry,....most of them are not happy without modification when you try and make them sew #138 thread. You will need to find a dual speed reduction pulley (so your thread doesn't heat and break), you will need to change the cam timing, needle timing, and needle clearance....and you made need to run compressed air to the needle tip (preferably titanium needles) for cooloing. oh, and you may have to "mitchell cord" open up the needle plate hole. The better advice on a tacker is to wait it out, and find a heavy duty, newer, servo controlled, programeable tacker. 3 axis if you can get it, but two axis will suffice. Try to get one of 20mm by 50mm field if you can get it. It should sew 138 with a dp 17 #23 needle and pull the lock thru the back side no prob (assuming you got your tensions right) Remember....bartacks are just lockstitches.....thus one can reproduce one with a PFAFF 138; 3 srtraight stitch passes, and then zig zag over. There is nothing magical about bartacks....other than the convience and consistent replication of a given strength stitch. Oh yeah, your bartacker should be able to do at least a 42 count stitch at 5-10mm wide on a 1 inch webbing. Also remember that bartacking is actually a weaker stitch theory than traditional straight stitch safety sewing (eg Box X, Or multi point W stitches (seatbelt, parachut harness stitch). I dont want to go into the theory about this here (im tired), but its true.....bartacks technically do more damage to the fabric your sewing and concentrate the strength vs distributing it over a wider area of fabric. Sailrite machines are kinda pricey for the quality and are now manufactured in china (quality has dropped)....they are good if you want walking zig zag...but a consew rb or rbl-2 or -3 would be better or the pfaff 138... good luck
-
Actually from the manufacturers actual abrasion resistance is higher than Nylon. However, Spectra, being very slippery, tends to catch on things easily....eg the thin fibers 'catch' on rock crystals and pull thru the nylon. Nylon locks upon itself better in the warp and weft....and thus are less likley to have strands pull. So in that way its a mute point...real world vs the lab...
-
-
-
http://www.dyneema.com/en_US/public/dyneema/downloads/DYNPR068E1006_Antifouling_Micanti.pdf
-
jfs1978....note the condtions of your pull test setup,...so we are not increasing our test variables as well. For example; did you pull over 9mm pins or larger or smaller? Also...for the most accurate results one should pull test identical new slings on your own equipment and then repeat after the usage timeframe vs relying on the manufacturers tag specs... (= much more controlled study) Also of note....in my opinion the slings attaching chocks, quickdraws etc dont offer enough elasticity to change the fall factor. But as soon as you get into one foot plus legth nylon slings, the elsasticity dramatically shows itself on the test bed. Note the ballistic Nylon in my pics stretching vs the all spectra harness pics being pulled.
-
Yes....looking back on my post...i did say "exposed to all different conditions". I do believe my statment is too broad as i am primarily referring to pure spectra exposed to the elements and workplace. While my products see lots of use in their respective industry...they are not neccessarily treated in the same manner as a climber's gear may be treated over years. And all my spectra is sewn with spectra thread vs the flex fatigue of knotting...and the 'pinch point' issue of knotting. So my statements should have been qualified... As pure Spectra slings are not a good choice for climbing (and not available as far as i have seen), i have not tested pure spectra slings exposed to the climbing environment; so jfs1978's mammut sling tests are not directley comparable to my tests (diff envrons and materials)... The most exposed and repetivley used pure spectra i have heard of is in the sailing industry.... but this is not my industry so actual info is second hand here... I will carry out some tests on ten year old, highly weather exposed pure spectra sewn slings in the next week and post the results so we can get to the bottom of this.
-
Dyneema = netherlands name for spectra Spectra = North America name for UHMWPE. (liscenced to Honeywell by DSM if i recall correctley) "Dyneema" is often mislabelled as the Nylon/spectra blended slings we see from companies like Mammut, onsight, etc... As regards jfs1978 test results.... i don't question your results; as, after 15 years of testing all different materials and scenarios i have found that there many variables involved that can effect differnet outcomes. Sometimes these variables are obvious, sometimes not. For example...my own test were on pure shuttle loomed, critical use, spectra 1 inch wide webbing, bartacked with pure spectra nylon thread. I then pull over minimum 9mm pins. Now, while these slings may have seen much environmental exposure, they were not "climbing" use slings and so may not have see the flexural exposure that your mammut's did. The Mammut slings will be a Nylon/spectra blend with Nylon bartacking (so product is not entirely spectra fiber)....this could possibly account for the loss vs pure spectra., given that the nylon is more prone to uv damage and etc... Yes,...i too have come across the data that reflects flexuaral degradation. Most of my products have not seen repetitive bending and flexing....so i should have qualified my results on that note (my apologies). Some studies have found that newer genrations of Spectra have less of a flex fatigue problem vs older spectra generations... And they have also found that initial loss in strength occurs at a certain rate, and then the loss decreases exponentially. I recentley set my shop back up, and put my pull testing facility back in action....so i will do some more testing and research into this area. I will sew up some pure spectra from old stock and new stock, using both old and new nylon thread. And i will bust some old slings i have kicking around. Ill post my results when i get done. And i'll video them and upload to you tube.