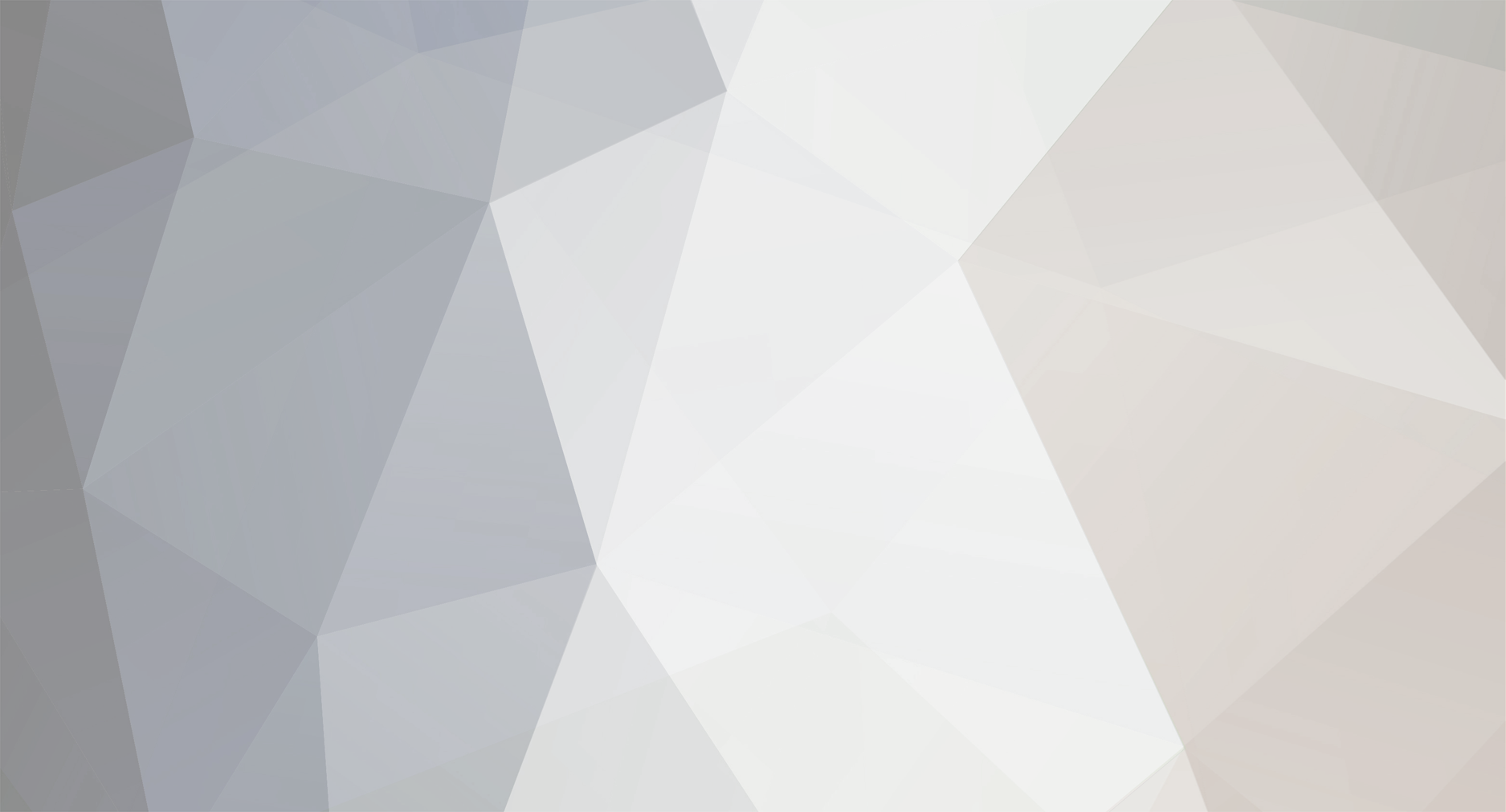
Patriot
-
Posts
6 -
Joined
-
Last visited
Content Type
Profiles
Forums
Events
Posts posted by Patriot
-
-
Exfoliation corrosion is not limited to aluminum only. Austenitic steels will show exfoliation corrosion. While I have my reservations that many, if any, hangers are made from carbon steel. Those made from stainless are prone for the same reasons as aluminum from the manufacturing processes working the grain boundaries.
-
My vote is for an intergranualar corrosion called end grain exfoliation. Think of end grain in wood sucking up water...the oxidization byproducts build up in between the grain layers of the material and it starts bulge and eventually flake.
-
www.tarptent.com
I dont have any personal experience with them, but have heard good stuff. Im looking at the Contrail for my uses.
-
FB does, you need the image location with the .jpg suffix.
Instead of:
http://www.facebook.com/photo.php?pid=30610302&id=1232002815
-
The hardness of the material isnt so much the hard part- as much as staying directly on the stud/bolt as you drill along its length. The rock as compared to the steel is soft and will allow the bit to wander off the bolt and into the rock. Compounded with the fact you have a drill bit sticking out that far and will bend and want to wander some regardless. Even on a machine drilling a 3.0 bolt out of a hole would be tricky. Material hardness in that Rockwell range can be drilled with a "normal" drill bit with ease- assuming power tools were used with a good feed/speed and some lube. Low rpms (<600 or less) and as much pressure as you can muster without breaking the bit, a little squirt of lube- you should be set. Hand drilling- better have some time on your hands...
The photo above is a pretty trick set-up. I dont think it needs to extract the bolt the full length from the hole. It should only need to travel maybe a quarter to half inch to break the bolt loose and would then be easy to pry the rest of the way out. You could make that assembly from aluminum to eliminate some weight. With a thicker cross section where the bolts thread thru, you could reduce the top plate considerably, and then the lower plate quarter inch thick would likely suffice.
[TR] A Summer Place - Mount Rainier National Park 9/30/2009
in Mount Rainier NP
Posted
The Naches Trail went thru that area.